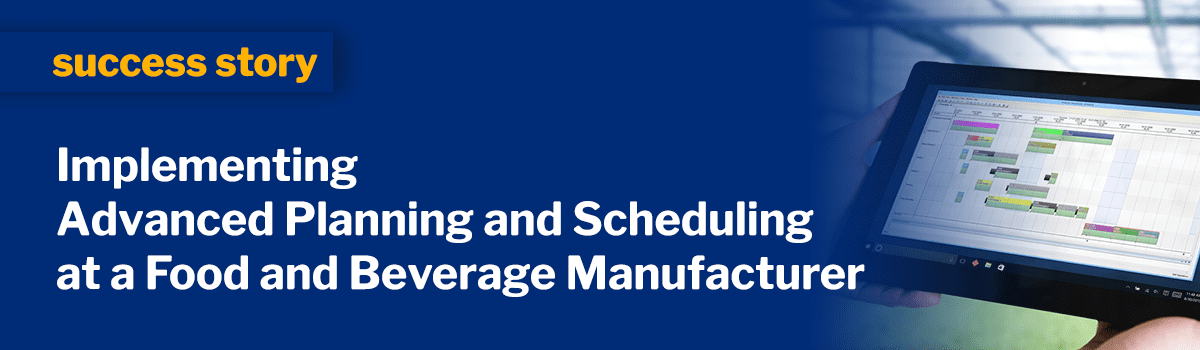
ATS was approached by a North American retail chain that needed to improve the planning and scheduling processes in one of its food and beverage manufacturing plants. They knew they could be doing more but realised that they didn’t have insight into the real capacity of the factory.
They also knew that they needed to react faster to change. This meant the ability both to see the impact of last-minute orders in the short term and to project seasonal sales demand over the long term.
Working with the Customer
ATS Global has a deep knowledge of Advanced Planning and Scheduling built up over more than 30 years. It was this experience that enabled the team to develop a path through the complex requirements of such a large project.
The ATS team provided consultation to the customer to understand their needs and chose to implement Opcenter Execution ( Discrete or Process) Opcenter APS as it was the solution that best fit with the customer’s requirements.
The Advantages of an Integrated Solution
Opcenter APS integrates beautifully with the customer’s ERP and MES systems so that it can leverage the existing information in the company. On the MES side, it can send order information to Opcenter Execution ( Discrete or Process) MES which is then able to send work orders to the shop floor.
The customer can also import sales demands with forecasts directly into Opcenter APS which allows it to simplify the entire production planning and scheduling process.
One Solution with Multiple Benefits
Using the powerful planning and scheduling algorithms available in Opcenter APS, the customer can now develop multiple, complex ‘what-if’ scenarios so that they’re better prepared for the unexpected.
It has also removed the large amounts of paperwork that were previously required for both planning and executing the production process. This is a benefit not just in cost but also for the environment.
And as with any digital solution, the availability of detailed, real-time information comes with several advantages. Not least of these is the ability to track and trace every individual lot through the manufacturing process. On top of this they have complete inventory management of their raw materials and finished goods.
With the system implemented, ATS is still working with the customer to provide support and ensure that they’re getting the most out of the solution.